IMPLEMENTACION DE HERRAMIENTAS
7 DESPERDICIOS MAS 1
1 correcciones
2 excesos de inventarios
3 sobreproduccion
4 excesos de movimientos
5 transportes innecesarios
6 esperas
7 procesos innecesarios
8 RR HH
DETECCION DE DESPERDICIOS
metodo de observacion

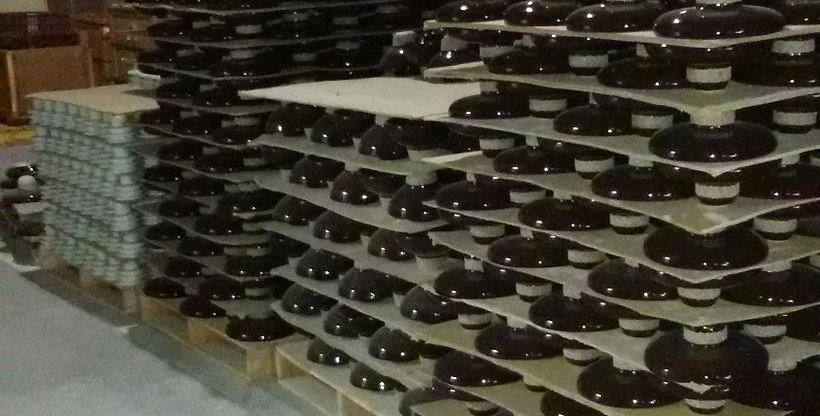
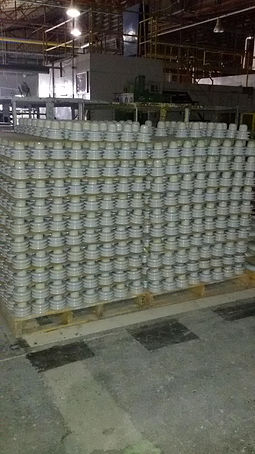

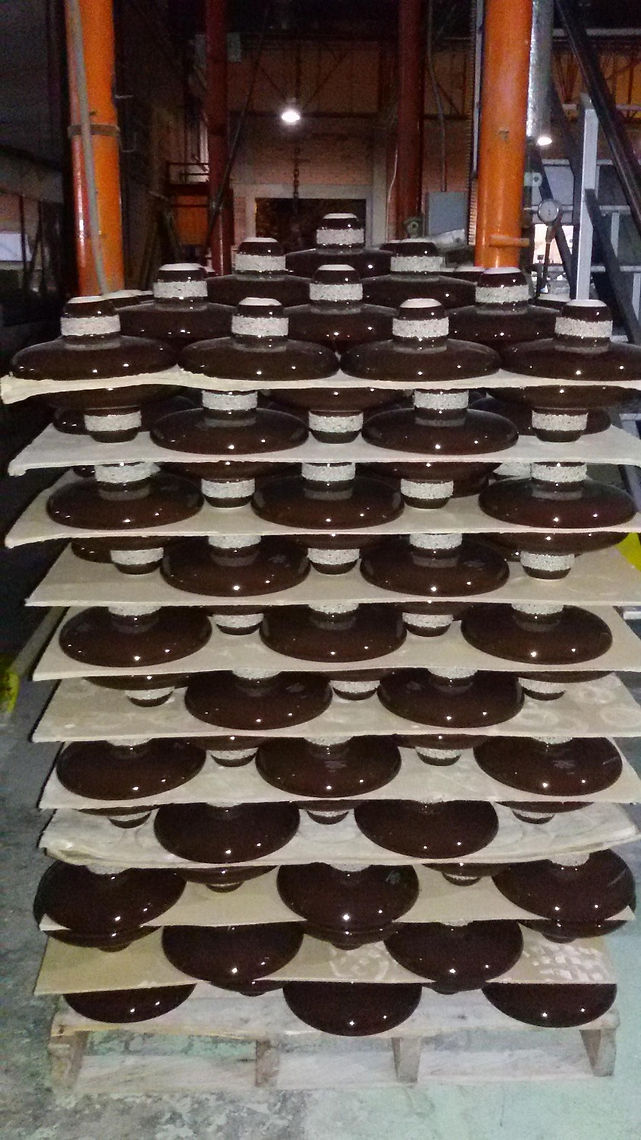
Identificacion de los desperdicios
En la seccion de acabados pudimos identificar varios desperdicios tales son: 1 sobreproduccion, 2 esperas, 3 exceso de inventarios y 4 exceso de transportes. la indagacion de proceso nos muestra muchos movimientos , distancias y esperas ineficientes que hacen que el producto sea mas costo y se demore mas al embarque, fuera del despilfarro de espacio ,tiempo, plataformas, estibas de madera y cartones dividiones para la acumulacion de la porcelana, quizas el no tener un sistema de personal disponible en los turnos podria llevar a este problema, pero podemos añadir que al reinventar el proceso podriamos eliminar los desperdicios.
reingenieria
EMPRESA: GAMMA ASLADORES CORONA
PROCESO IDENTIFICADO: ACABADOS
Los cambios propuestos son para clientes internos
Identificamos los clientes los cuales son revisión, chequeo eléctrico, empaque y logística y transporte
Caracterización:
-
Dueño del proceso: jefe de sección de acabados
-
Entradas : producto en proceso
-
Salidas: producto empacado listo para despacho
-
Medios: software, máquina de chequeo eléctrico, bpcs, wms, radiofrecuencias
-
Recursos: materia prima, herramientas de implementación.
-
Clientes: logística y transporte
-
Proveedores : carga y descarga de hornos
-
Indicador: numero toneladas al almacén
Paradigmas:
-
Aumento de carga laboral
-
Aumento de posibilidades de enfermedades profesionales
-
Cansancio físico y mental
-
Persecución laboral
Brecha (distancia)
El proceso de acabados tiene muchos desperdicios y problemas de sobreproducción, exceso de transporte, exceso de inventarios y esperas, lo que buscamos es acortar esos tiempos y procesos que no agregan valor para tener un tiempo mucho más competitivo hacia la entrega del producto al cliente final.
En el cuadro identificamos en un lote de producción 43 minutos y 76 metros recorridos entre transporte y almacenamiento innecesarios que es lo que queremos mitigar en el proceso. Las esperas del proceso son muy grandes ya que pueden pasar días o semanas por falta de suministros o procesos adicionales que se presentan, además de la falta de mano de obra en los diferentes turnos.
diagrama de flujo de acabados
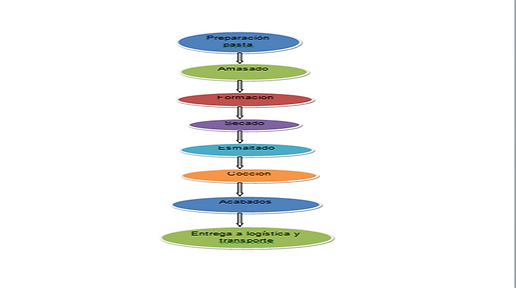

DIAGRAMA ACTUAL DEL PROCESO
PROPUESTA
diagrama de fkujo de ailadores electricos
Montar un sistema con bandas transportadoras en flujo continuo con personal en los tres turnos del día para eliminar los transportes incensarios, esperas y excesos de inventarios ya que eliminaríamos 43 minutos y 76 metros de recorrido por lotes de producción, minimizando los riesgos de accidentes y la carga laboral


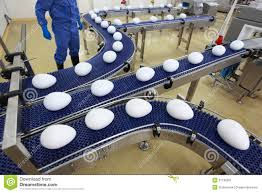
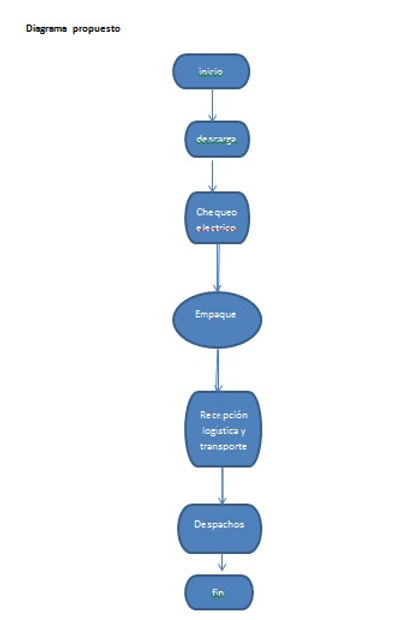